What Is Bill of Materials (BOM) & How to Create One?
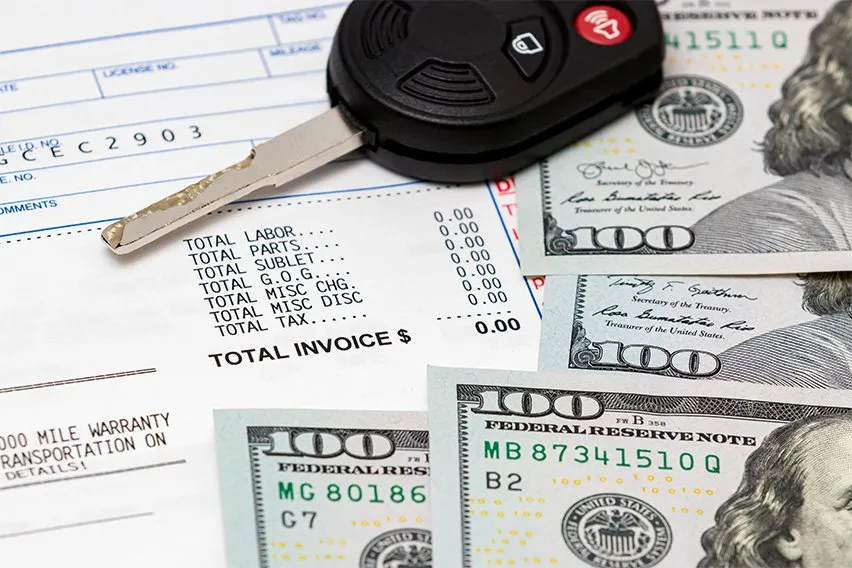
If your business is dependent upon making items from raw materials, then you may benefit from bills of materials. These documents are a comprehensive list of everything needed for a finished product. However, they may be better for your business than you think. Learn about bills of materials and how to create them in this article!
Here’s What We’ll Cover:
What is a Bill of Materials (BOM)?
Things to Consider When Creating a BOM
What is a Bill of Materials (BOM)?
A bill of materials, or BOM for short, is an extensive list used by manufacturing companies. These lists are highly detailed, and contain everything needed for a company. They are normally sorted into comprehensive levels. At the top you’ll find the finished product, and at the bottom you’ll find the raw materials. When reviewing a BOM, you can expect to find any and all of the following:
- Parts
- Specific items
- Assemblies
- Subassemblies
- Intermediate assemblies
- Related documents
- Product drawings
- Process of assembly
- Any other requirements to create a product
BOMs are used for complex products. You wouldn’t expect to find them for simple items. Rather, they’re used for products that require some level of engineering. There are single-level bill of materials (single-level BOM) as well as multi-level bill of materials (multi-level BOM). A multi-level BOM is normally organized by rank. The highest levels of the product are at the top. The individual pieces are at the bottom.
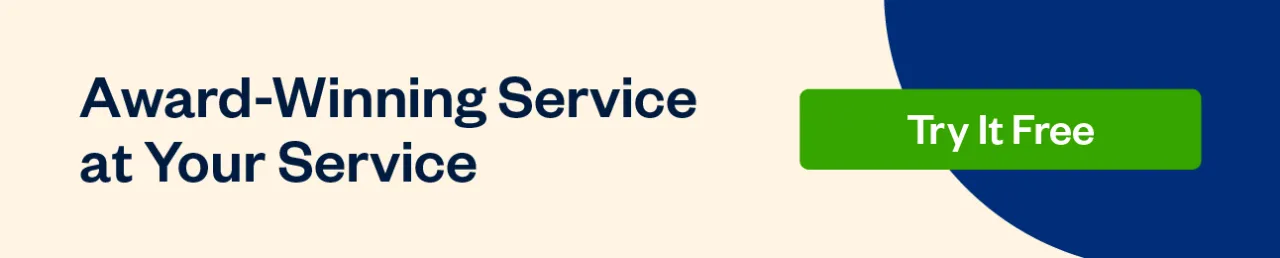
All Companies That Build Products Use BOM
Any company that builds its products refers to the BOM. In fact, the first part of the design process for any manufactured product is creating a BOM. This document will be the resource used to create the products it is related to.
A simple way of looking at it is by thinking about a recipe. The end result is the food that you make. However, to make the food you need the list of ingredients and the instructions. A BOM is a recipe for a product.
Why is a BOM Important?
Most products that require a BOM also rely on an assembly process. This assembly process needs structure to work smoothly. It consists of all of the materials and processes required to make final products. If a BOM is not accurate, the assembly process suffers. If this happens, then the overall business processes.
A current example of how crucial the assembly process is can be seen in car manufacturing companies. Throughout the pandemic, product shortages have been common. Some of the most common shortages are computer components. Without these computer parts, the vehicles being made cannot function. Because car companies knew that these parts were integral, they stopped production of certain vehicles. The reason they were able to stop these processes is because they had a BOM to refer to.
A BOM is Necessary for Enterprise Resource Planning (ERP) and Materials Requirement Planning (MRP)
Both ERP and MRP need a BOM to be designed. A BOM tells both of these processes what the needs for a product are. For ERP, it delegates expenses and financial requirements. It does the same thing for MRP, but focuses on only the raw materials required for products.
BOMs are Displayed in Two Ways
A BOM can be displayed in one of two ways. The first is called the explosion display. An explosion display shows an assembly at its highest level broken down into parts. It breaks assemblies as far down as the lowest level available.
The other method of display is the implosion display. An implosion display shows a product at its individual parts. It then links these parts to assemblies to explain how the product is put together.
How is a BOM Created?
A BOM is part of the design process. It is created by breaking a product down into its simplest materials, then explaining and displaying how they are connected. There are a number of requirements for every BOM made. Any BOM without the following information included is considered incomplete.
BOM Level
Every part or assembly of the product needs to be assigned a BOM level. The BOM level is a number that explains where the part fits into the hierarchy of the product. Anyone who understands the BOM structure can then understand the part’s importance and fit in the bill itself.
Part Number
All parts of a product need an individual part number. This allows manufacturers to reference and identify individual parts quickly. Part numbers are part of a numbering scheme. Number schemes can be intelligent or non-intelligent. Intelligent numbers have meaningful information in each part number. Non-intelligent numbers do not, hence the names.
Part Name
In addition to part numbers, parts also need names. This is another method of quick part identification.
Phase
Every part of a product that’s being manufactured should be given a designated phase. This phase describes where the part is in its lifecycle. Common terms are ‘In Production,’ ‘Unreleased,’ and ‘In Design’. This helps with creating product timelines, an integral part of any new product introduction.
Description
Every part and assembly of a product needs a detailed description. Descriptions should help manufacturers distinguish similar parts from one another.
Quantity
Every part needs to have a quantity assigned to it. The quantity should be the total number of parts needed for assembly and subassembly.
Unit of Measure
When creating a product, the units of measure need to be the same for the entire product. This means selecting a measurement system and sticking to it. If some parts are described in feet, then smaller parts have to be measured in inches. Another common measurement is ‘each,’ meaning the number of parts used in each build.
Method of Procurement
How are the parts going to be procured? Each part needs to be obtained somehow. Off-the-shelf and made to order are the most common designations.
Reference Designators
This applies to products using printed circuit board assemblies (PCBAs). These need to have reference designators showing where parts fit on the board. This eliminates confusion during the assembly process.
BOM Notes
Any notes pertaining to the BOM should be included. These notes help people working on the BOM together communicate with one another. It also keeps everyone on the same page.
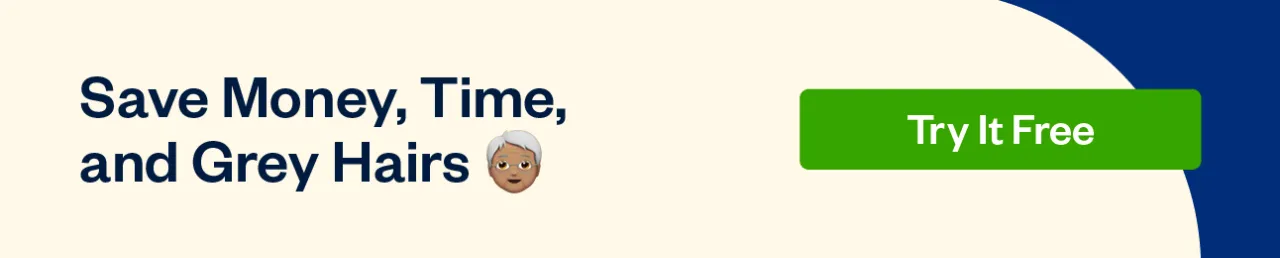
Things to Consider When Creating a BOM
When manufacturing companies make a BOM, they tend to struggle with the same things. When making a BOM, be sure to take the following into consideration.
- Consumables: Make sure consumables are in your BOM. If they aren’t in the BOM, they may not make it into the product. This includes things like glue and fasteners.
- Attaching Files: All BOMs will have additional files. Make sure all people working on the BOM know where the appropriate files belong.
- Users: People who are creating the BOM will not be the only people to use it. A high level of detail should be used so that there is no confusion for users. It should be easy for everyone.
- Reconciliation: Products change over time. As such, so will a BOM. When products change, your BOM needs to change with them. If it doesn’t, then confusion will be created when assembling the product. Confusion can lead to a shutdown of the assembly process. No manufacturing company wants that.
Key Takeaways
A BOM is a product’s recipe. Every part and instruction should be included in a BOM. If information is missing, then it’s likely that products will be incomplete. A thorough BOM is the first step to manufacturing any product. Make sure yours is as detailed as possible! Our resource hub has plenty more information like this. Be sure to visit it for all your business information needs!
RELATED ARTICLES