Difference Between Job Costing and Process Costing
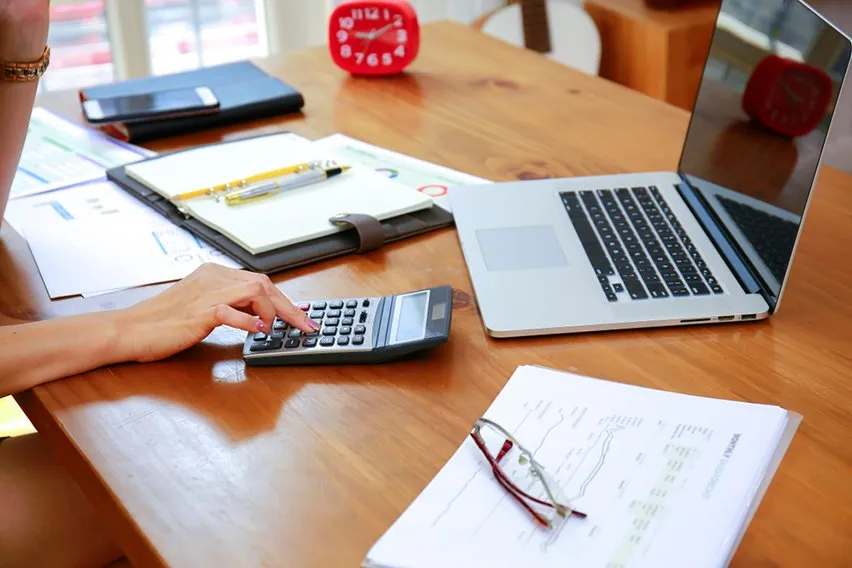
As an organization, your primary objective is to generate profits; returns for shareholders. However, it’s not just about that. The profits you earn are intrinsically related to sales volumes and revenue. In fact, you may have high sales volumes and revenues but very little or no profit.
How’s that possible?
Well, it comes down to your costs. A key element of becoming profitable and scaling is effective cost management. It helps in different ways that ultimately translate to a higher profit margin.
When it comes to measuring the cost of products, you can either use job costing or process costing. These are types of accounting systems. Companies use them to track all the costs they’ll incur when delivering a service or producing products. The accounting system you should use depends on the nature of your business.
Read on to learn about these two cost accounting techniques and how they compare.
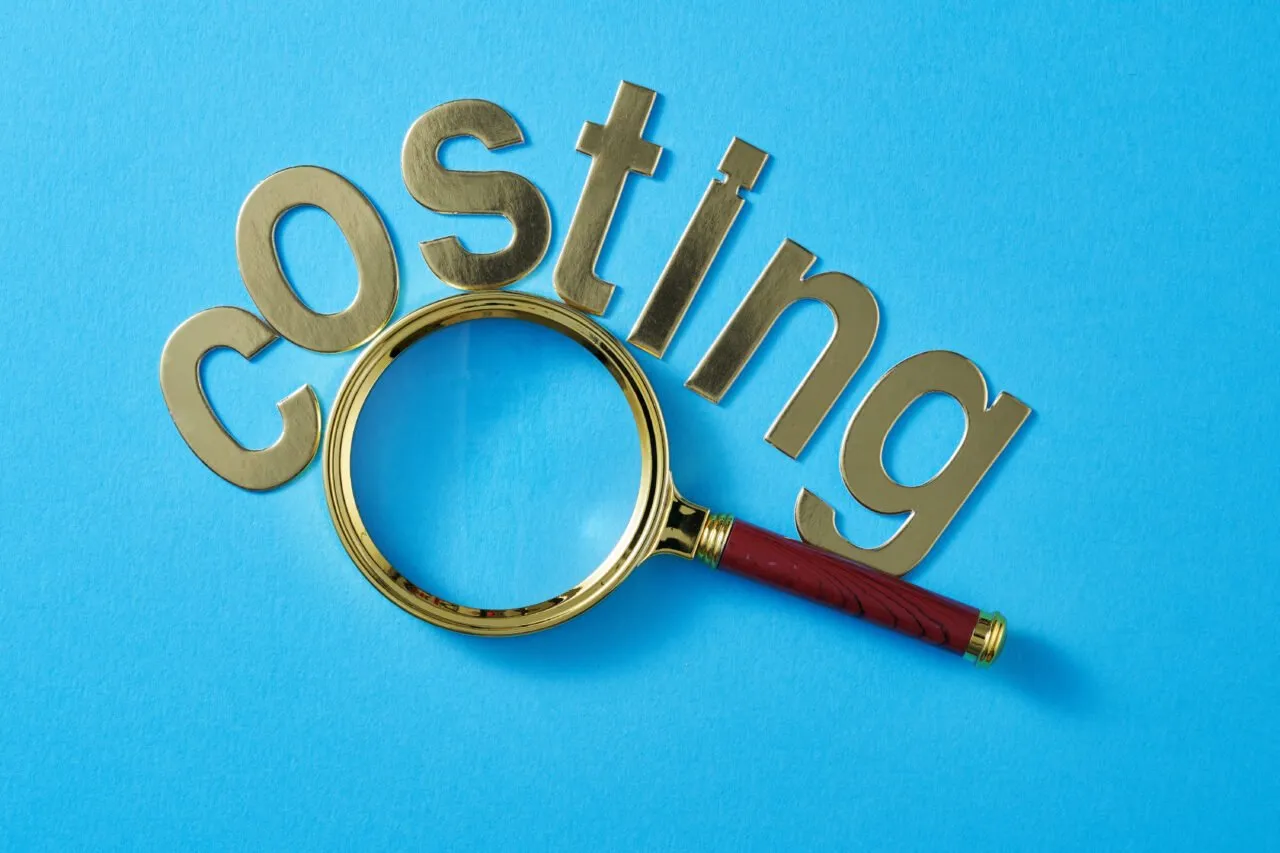
Here’s What We’ll Cover:
Differences Between Job Costing and Process Costing
What Is Job Costing?
Job costing is also known as job order costing. It’s ideal for the service industries where institutions work on a project basis, as the total cost varies with each job. Often, such professional services involve the need to provide customers with accurate estimates before the work begins. These include freelancers, movers, mechanics, and plumbers.
Some of the features and factors that affect direct costs with job order costing include:
- The unique needs of the job
- Specific requirements or needs that the client may have
- Variances in how the work progresses across different phases
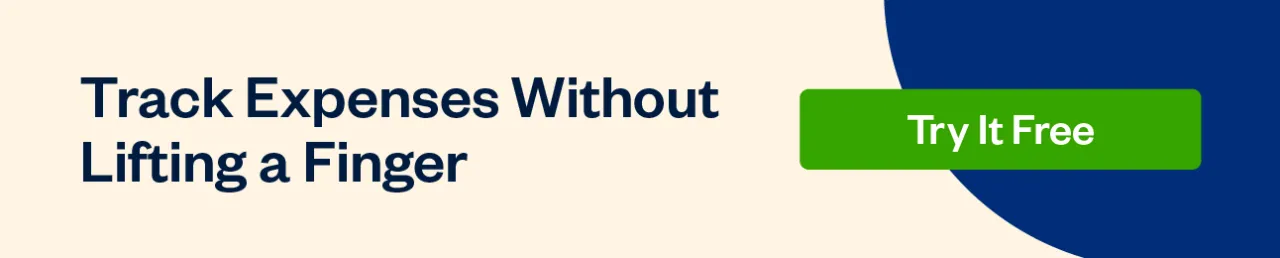
Assume that two people with similar kitchens hire a construction company to perform a similar renovation. The project manager will begin by estimating the cost of individual elements of the project. These include:
- Direct material cost
- Direct Labour costs
- Equipment costs
- subcontractors
They’ll tally the estimates for each factor to get the exact cost for the whole project.
However, despite all the similarities between individual projects, the costs will vary. This is because other variances will arise during the project and can only be accounted for at that time. For example, they may find that the entire plumbing system for one house is damaged. This means they may have to replace it, further increasing costs.
Given the nature of such projects, job costing systems are ideal. They help the contractor capture the actual cost of each job. In turn, this also allows them to have an accurate expectation of profits.
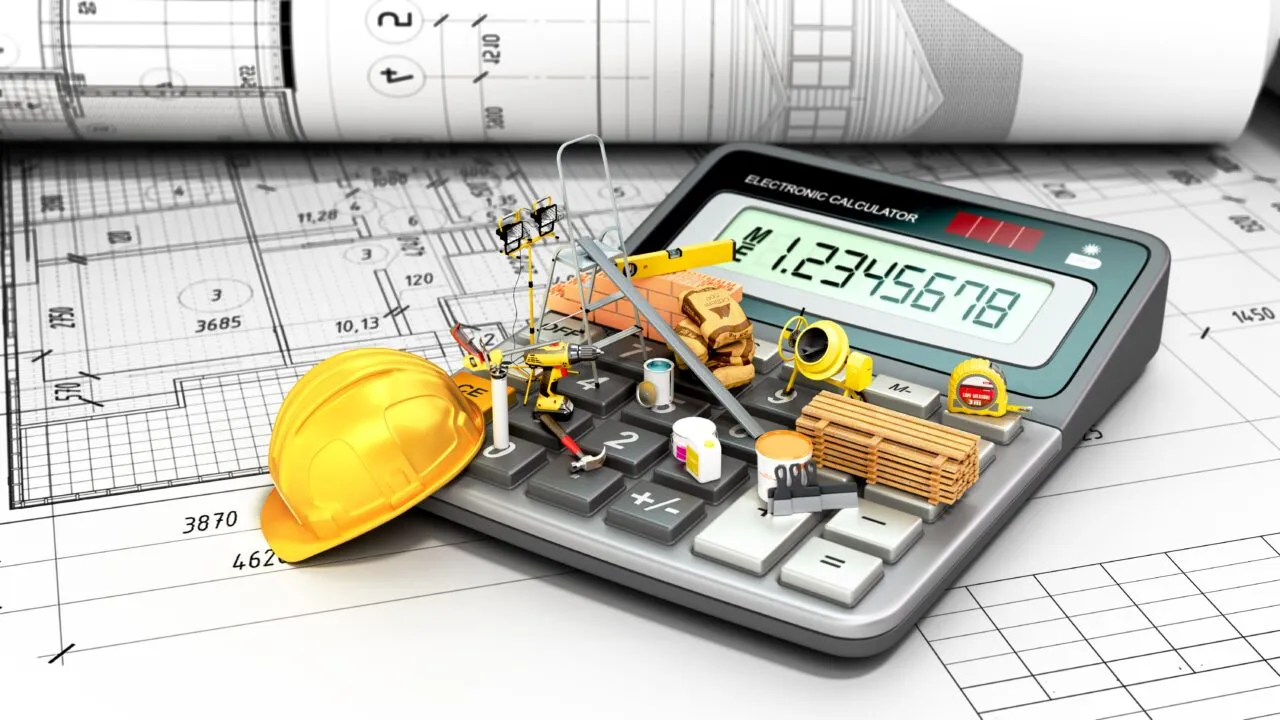
For effective job costing, there are different costs that you should account for. They include:
- Direct labour costs- Includes the cost of employing people but not management and administrative costs
- Direct material costs- Inclusive of all the direct materials necessary for a particular project
Along with the direct labour expenses and material costs, job costing also accounts for overhead costs. These include indirect expenses you incur for the job. They include:
- Cost of management and administrative work
- Cost of travel to and from the job site and time taken
- Cost of tools and equipment such as nail guns, ladders, etc.
- Material costs across projects
- Insurance costs
- Marketing costs
- Unexpected costs
Compared to direct labour and material costs, figuring out the overhead costs can be challenging.
Pros of Job Costing
For organizations that use job costing, there are several benefits to be enjoyed. They include:
- Easier to make comparisons between the cost and profit- With such jobs, you can create a great estimate for how much you’ll spend. Comparing it with how much you’ll earn allows you to determine the profit.
- Gives you pricing flexibility- From the word go, you’ll have a clear picture of the costs, income, and profits. This allows you to determine the appropriate sale price and know the discounts you can offer without compromising profits.
- Enables you to measure productivity- If you know the specifics for the project, you can determine how long your team should take to complete it. If they take longer than that, you will know that something needs to be addressed before the next job. Also, it’ll help you realize the variance in productivity among employees.
- It makes budgeting easy- You’ll have a rough idea about the various costs you’ll incur for the type of jobs you handle. As a result, creating a company budget for each period is easier.
Cons of Job Costing
Regardless of how beneficial job costing is, it also has some drawbacks. These include:
- It can be labour intensive
- It does not help with controlling costs
- Requires a lot of paperwork and documentation
- Some guesswork is involved
What Is Process Costing?
When dealing with near identical products and services, process costing is the ideal cost accounting method. It’s especially effective for the large-scale production of homogenous products.
As the name suggests, you’ll account for different processes. These are the stages at which raw materials are converted into another identifiable form. As such, you’ll have to divide the plant-based on various processes. They may either be performed parallelly, sequentially or selectively.
Therefore, each process will require a process account. With this, the output of an individual process becomes the input of the next one. This goes on until you attain the output of the final process, which will be the total cost of the product.
This form of cost accounting is suitable for large-scale production, companies that produce different products, or where there are various levels of production. These include companies that produce soap, paper, steel, paints, and cold drinks.
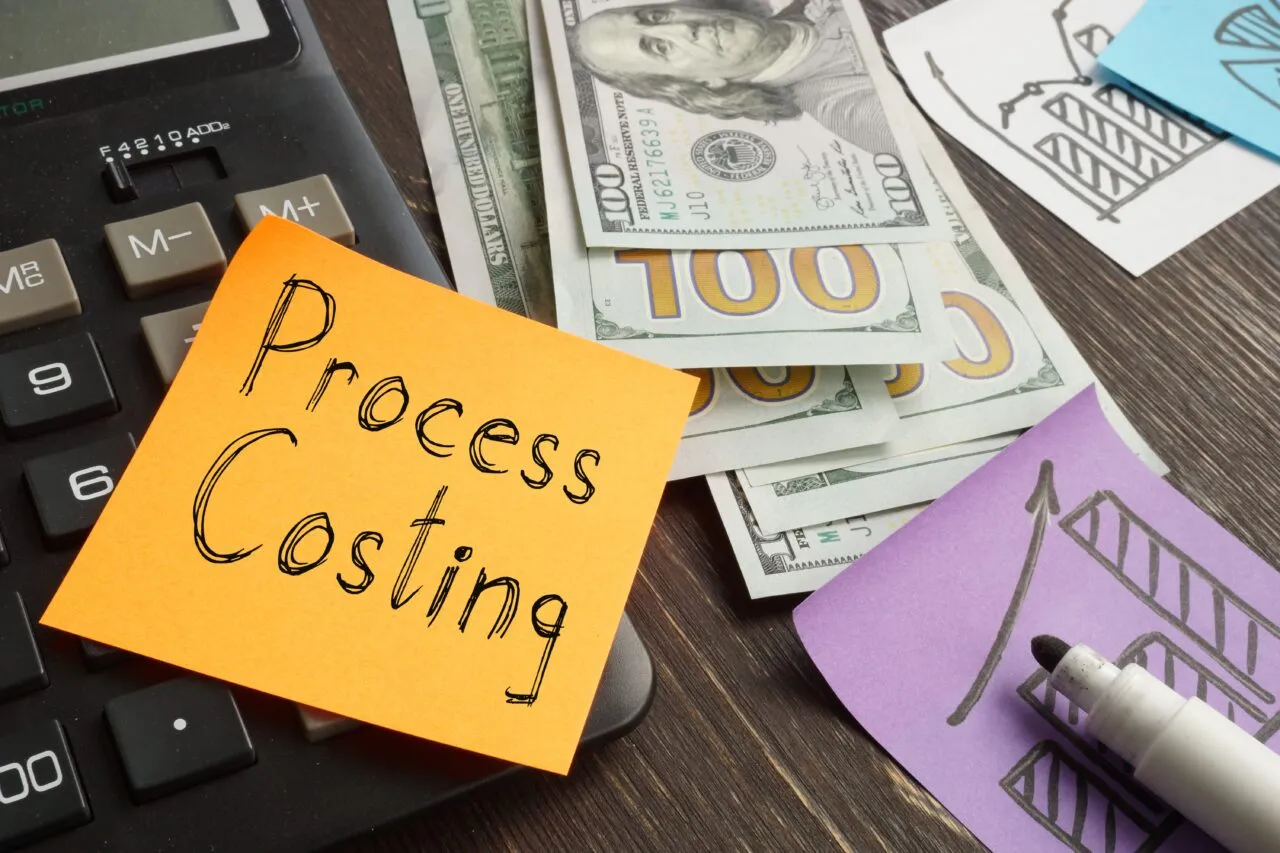
Pros of Process Costing
Process costing offers organizations benefits such as:
- Easy to use- Since there’s standardized products and processes, so too are the costs, making process costing systems easy to use.
- Flexibility- With process costing, companies enjoy flexibility in the production process. Should there be a need to make adjustments, you can simply add or remove a process. In doing so, you can reduce production costs and increase profitability.
Cons of Process Costing
As with job costing, process costing also has some disadvantages. These include:
- Cost errors- One of the drawbacks of cost accounting is that there are multiple ways costing errors may occur. Since it does not use direct allocation costing, it’s possible for non-production costs to be included. Also, the products may be under-costed if accounting teams do not account for all production costs. If this happens, your profits will be lower.
- Equivalent units- Equivalent units are the unfinished goods that remain at the end of an accounting period. These must be accounted for in cost accounting and are often an estimate or guess. Any inaccuracies translate to inventory management challenges and determining the number of finished products available for sale.
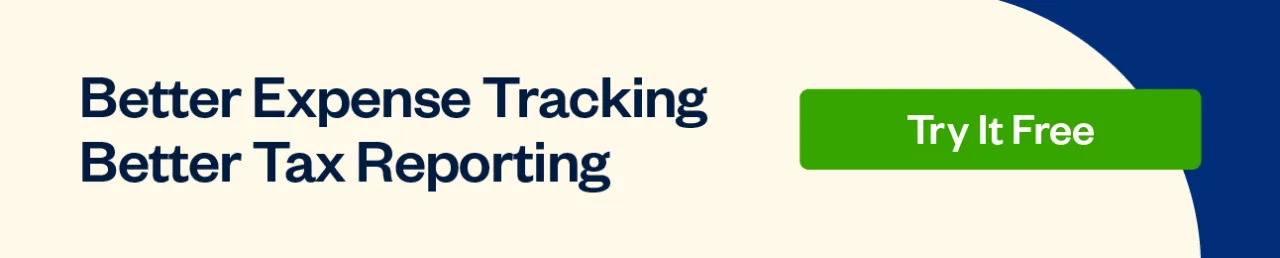
Differences Between Job Costing and Process Costing
As you now know, job costing and process costing use varying approaches to calculating the cost of individual products and services. Therefore, they have differences such as:
- Assignment- In process costing, you first determine the cost of each process, add them up and calculate based on the number of units. On the other hand, job costing calculations are done based on each job.
- Production- Production is standardized with process costing, while for job costing it’s customized.
- Cost transfer- While you can transfer some product costs from one process to another in process costing, that cannot be done with different jobs in job costing.
- Reduction in cost- Job costing does not offer as many scope of cost reduction as process costing.
- Individuality- Since each job is different, you can produce custom products in job costing. However, there is no individuality with process costing as it involves the production of identical units.
- Losses- It’s possible to separate losses with process costing, but it is not possible with job costing.
- Size of job- Process costing is ideal for large scale production, while job costing is best when the production units are small.
- Work in progress- At the beginning and end of each period, there’s always work in progress (WIP) with process costing. With job costing, there may or may not be WIP.
- Recordkeeping- With job costing, recordkeeping is time-consuming and tedious. However, it’s more streamlined and efficient with process costing.
- Industry- Process costing is a suitable option for industries where products are standardized and produced in mass. For sectors where consumers have room to customize products and services to their liking, job cost is suitable.
Key Takeaways
When it comes to job costing and process costing, it’s not about which is the best. Instead, it is about the one that suits your construction company better. The most important thing is tracking your product costs accurately with either one. While you can do so manually, it’s best to have a solution you can trust.
FreshBooks is a software solution that provides a host of accounting solutions. These include cost tracking, invoicing, time tracking, etc. Try it for free today to find out more about how it can help grow your company.
If you enjoyed reading this article, check out more articles like this on our Resource Hub!
RELATED ARTICLES